von Reinhard Wirtz
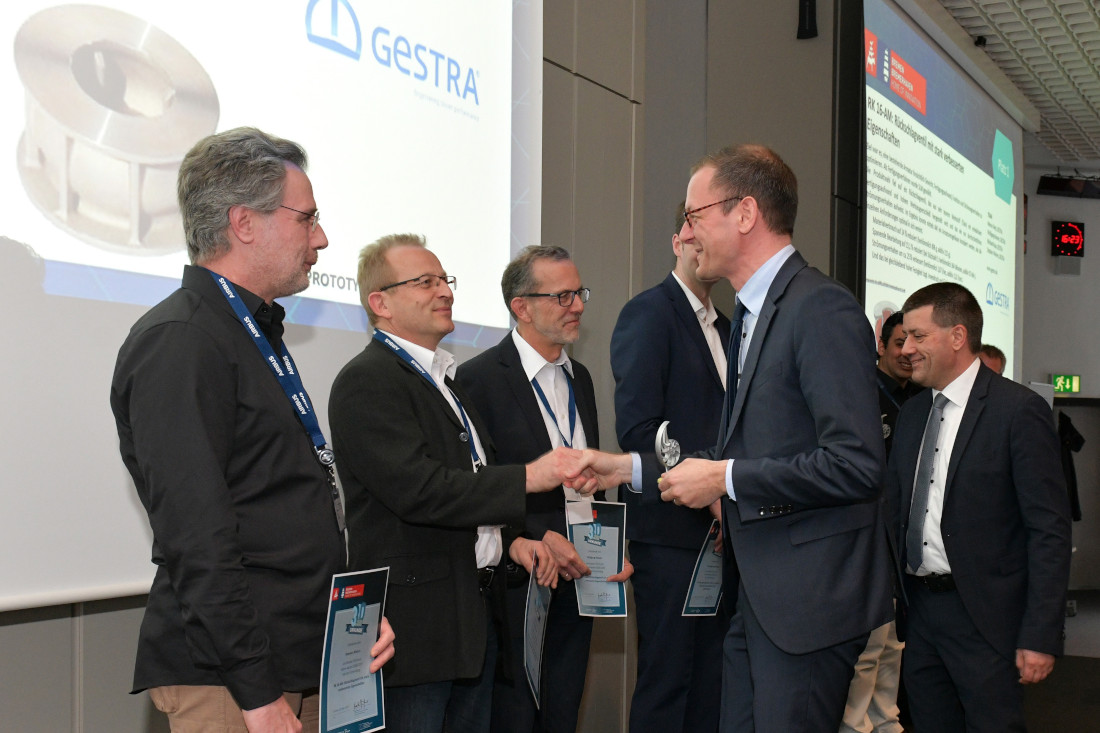
Neugierde, die sich auszahlt: Stephan Winters, Michael Kopa, Wolfgang Hansen (v.l.n.r.) werden mit dem Bre3D Award vom Bremer Wirtschaftssenator Martin Günthner ausgezeichnet. - Bild: SWAH
Am Anfang war die Neugier. Wolfgang Hansen, Stephan Winters und Michael Kopa, drei Ingenieure beim Bremer Armaturenhersteller GESTRA, begannen vor einigen Jahren aus reiner Neugier, Einzelstücke aus Kunststoff zu drucken und erste Erfahrungen mit dem 3D-Drucker zu sammeln.
Als sich das Experten-Trio damals auf den Weg machte, geschah das auf eigene Initiative und abseits der Routineaufgaben im Unternehmen. Triebfeder war die Neugier, berichtet Michael Kopa, einen Auftrag der Geschäftsleitung gab es nicht.
Den GESTRA-Ingenieuren wurde allerdings schnell bewusst, dass der Verwendung von Kunststoff im Armaturenbau enge Grenzen gesetzt sind. Denn häufig gilt es bei der GESTRA AG Baugruppen zu liefern, die hohen Beanspruchungen durch Dampf, Temperatur, Druck oder chemische Prozesse standhalten. Sie mussten mit Metall drucken, sollten die Armaturen dem standhalten.
Im Bremer Netzwerk fündig geworden
Vom ehemaligen GESTRA-Vorstand Lutz Oelsner erhielten sie den Tipp, sich mit Peter Sander von Airbus in Bremen auszutauschen, einem weit über die Bremer Landesgrenzen hinweg bekannten Experten und Promoter des Zukunftsthemas „additive Fertigung“. Er zeigte ihnen den Weg in den Metall-3D-Druck – genauer gesagt, den Titan-Druck.Kostspieliger Exot
Als erstes Bauteil für den Titandruck nahm sich das Team „RK 16-AM“ vor, ein so genanntes Rückschlagventil. „Das ist bei uns eigentlich eine Standard-Armatur, die wir in verschiedenen Ausführungen fertigen“, sagt Maschinenbauer und Diplomingenieur Wolfgang Hansen. Für Kunden aus der Chemiebranche könne die Armatur allerdings nicht aus den üblichen Werkstoffen gefertigt und geliefert werden, da häufig chemisch aggressive Substanzen wie Salzsäure, Salpetersäure oder feuchtes Chlor eingesetzt würden. „Für solche Einsätze stellen wir das Rückschlagventil aus Titan, einem sehr teuren, schwer zu bearbeitenden Werkstoff, her. Das Bauteil muss dann mit einem erheblichen Fertigungsaufwand unter hohem Werkzeugverschleiß abseits unserer Serienfertigung als Einzelstück produziert werden“, erläutert Hansen. Das koste Zeit, da komme es allein durch störende logistische Abläufe zu erheblichen Verzögerungen. Und die Spezialanfertigung in kleinen Stückzahlen behindere die übrigen Serienproduktionen.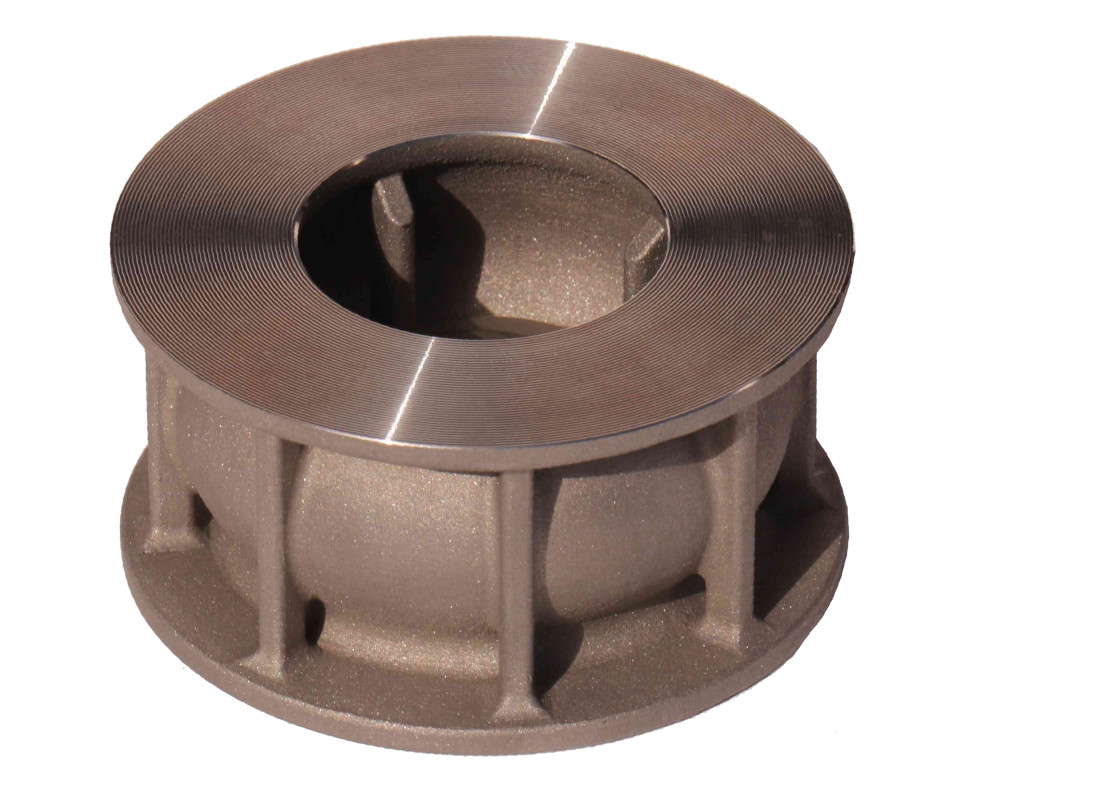
Durch den Einsatz additiver Techniken konnten die Ingenieure enorme Einsparungspotenziale in der Fertigung des Ventils erzielen. - Bild: Gestra AG
Konstruieren neu denken
Der Druck des Werkteils in Titan erforderte komplett neue Prozesse. „Wir haben versucht herauszufinden, welche Vorteile dieses Verfahren bietet“, beschreibt Wolfgang Hansen das Vorgehen. „Wir haben dabei festgestellt, dass sich durch den Einsatz additiver Techniken der Konstruktionsprozess verändert, denn hierbei kann man der Funktion des Bauteils folgen und seine Funktion in den Mittelpunkt stellen. Das Bauteil wird rund um diese Funktion herum modelliert. Es werden Strukturen möglich, an die mit subtraktiven Fertigungsverfahren nicht zu denken ist.“ Das Ergebnis kann sich sehen lassen: Der Materialverbrauch sank um 76 Prozent, die Bearbeitungszeit bei einer Stückzahl von 1 um 85 Prozent, das Strömungsverhalten verbesserte sich um ein Viertel. Schon diese Reduktion auf wenige technische Daten erzeugt bereits eine Vorahnung von dem Potenzial der neuen Fertigungstechnologie.Neuland für Zertifizierer
Deutlich wird: Additive Fertigung kann einen kräftigen technologischen Sprung nach vorn bewirken. In Kombination mit Digitalisierung und künstlicher Intelligenz ist man geneigt, von einer technologischen Revolution zu sprechen. Gleichwohl verpasst GESTRA-Konstruktions- und Fertigungsexperte Michael Kopa der Annahme, nun könne sich alles blitzschnell wandeln, einen pragmatischen Dämpfer: „Wir können unser Gerät so noch nicht auf den Markt bringen, weil wir europäischen Regulierungen unterliegen, deren Vorgaben zwingend vorschreiben, wie Werkstoffe beschaffen sein müssen. Wir müssen uns das von einer Zertifizierungsstelle bescheinigen lassen. Das ist auch für zertifizierende Institutionen wie den TÜV oder Lloyd's Register Neuland. Auch sie beginnen jetzt, mit uns zu lernen.“ Kopa und Hansen machen deutlich, dass dieser Vorgang durchaus schon einmal zwei Jahre in Anspruch nehmen kann. Zwar ist die GESTRA AG selbst Mitglied eines DIN-Ausschusses, der die Normen für die Regulierung festlegt. Auch profitiere man vom fachlichen Austausch unter den Ausschussmitgliedern. Aber beschleunigen lasse sich die Prozedur dennoch nicht, und schließlich wolle jeder sein eigenes Produkt entwickeln, vorbehaltlose Offenheit sei hier eher nicht zu erwarten.Auszeichnung beim 3D-Award
Bis dahin es soweit, kann das Team aber einen anderen Erfolg feiern: Den Gewinn des ersten Bre3D-Awards des Senators für Wirtschaft, Arbeit und Häfen in der Kategorie „Funktionsintegration“. Dass das Trio schon bei seinem ersten Antritt in der additiven Fertigung von Metall-Werkstücken eine Auszeichnung und einen der vordersten Plätze im Wettbewerb erringen konnte, hat die gewieften „alten Hasen“ bei der GESTRA AG überrascht und gefreut.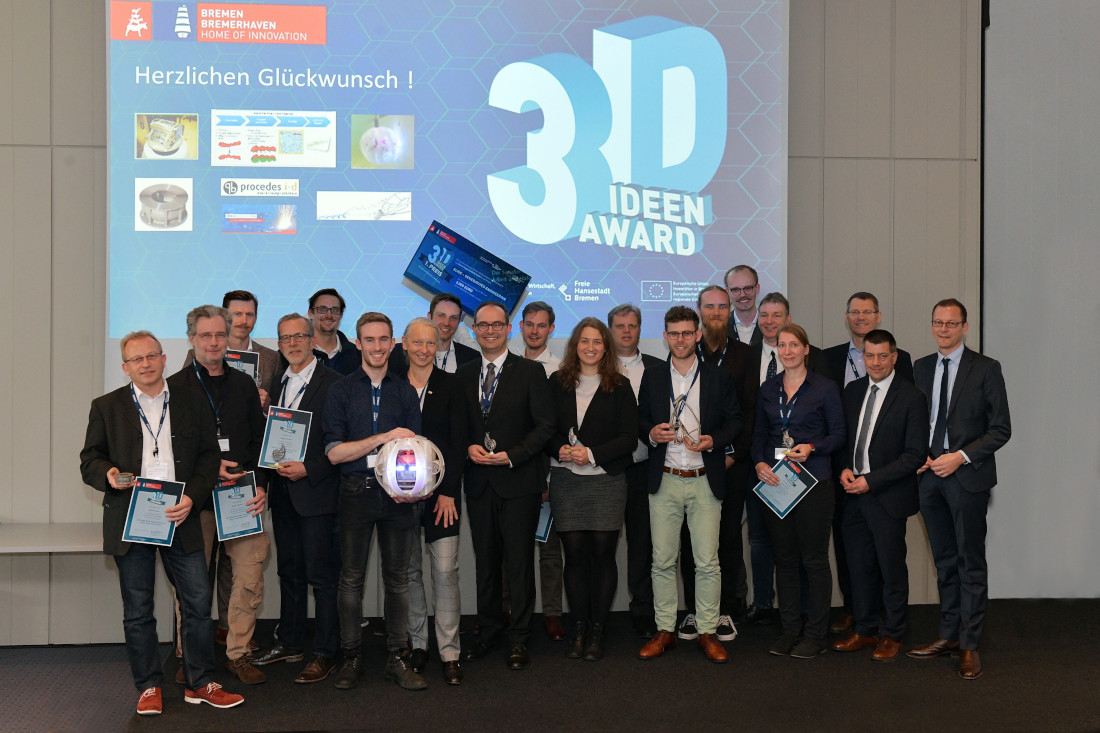
Das erste Mal angetreten und direkt ausgezeichnet: Das Trio der Gestra AG gewinnt den Bre3D Award in der Kategorie "Funktionsintegration" - Urheber: SWAH
Überblick: 3D-Druck
Zerspanen, drehen, fräsen, hobeln, bohren, schleifen, polieren bis es passt – ein grobes Materialstück verwandelt sich in ein präzises technisches Bauteil oder eine Baugruppe. Seit Generationen folgt die industrielle Fertigung – und nicht nur sie – diesem Produktionsschema („subtraktive Fertigung“). Die neuerliche Idee des 3D-Drucks, vom „Hinzufügen statt Wegnehmen“, ist von genialer Schlichtheit: Material wird Schicht um Schicht aufgetragen, bis das Werkstück hervortritt („additive Fertigung“). Bremen ist ein Hotspot des industriellen 3D-Drucks und fördert das Thema mit der Ausrichtung des Bre3D-Awards.