von Jann Raveling
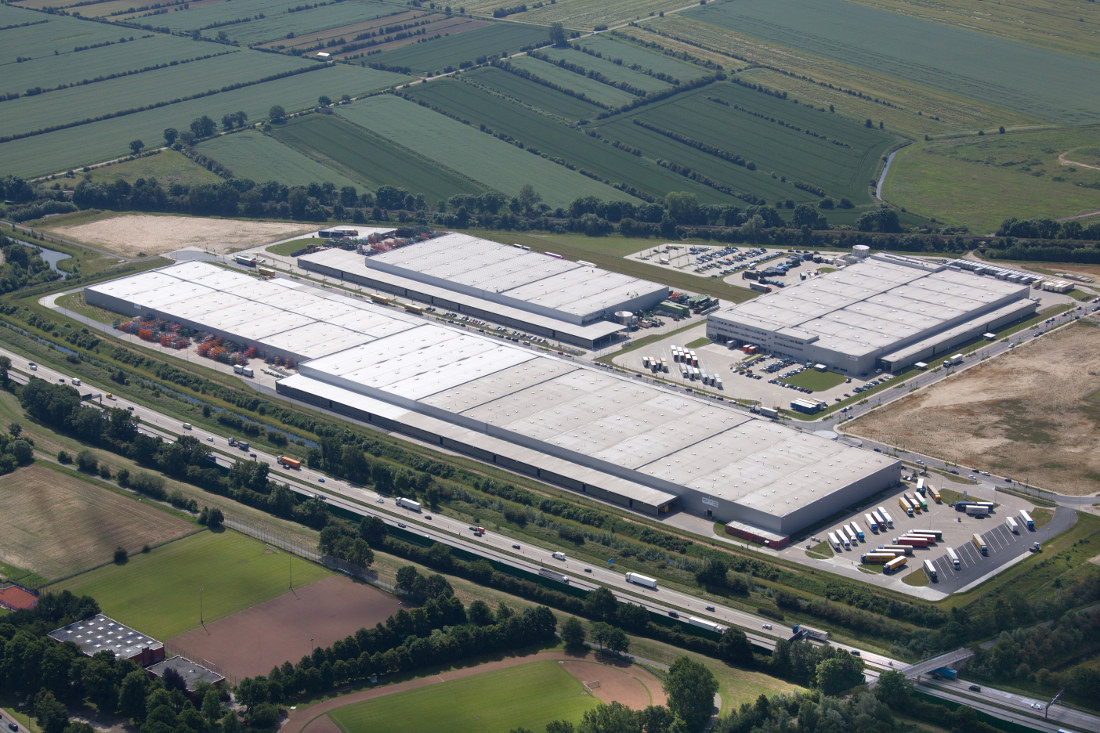
Über zwei riesige Hallen erstreckt sich das LOREL Gelände im Gewerbepark Hansalinie © LOREL Logistik GmbH
Die LOREL Logistik GmbH betreibt in Gewerbepark Hansalinie das Plant Consolidation Center. Die Aufgabe des Logistikzentrums ist es, die Komponenten und Einzelteile der Zulieferer zusammenzuführen und zur richtigen Zeit im nahen Mercedes-Benz Werk bereitzustellen.
Wer sich in den Hallen von LOREL bewegen möchte, braucht ein Fahrrad. Denn die beiden Hallen messen knapp 100.000 Quadratmeter überdachte Fläche – mehr als 13 Fußballfelder. In ihnen arbeiten 600 Angestellte im 3-Schicht-Betrieb, die pro Tag 9.000 Ladeeinheiten von den Lieferanten entgegen nehmen und in der Folge auch wieder versenden, sowie 100.000 Einzelteile sequenzieren. Insgesamt 90 Prozent der Teile für die Mercedes-Modelle werden über LOREL an das Werk geliefert – in 360 LKW-Fahrten pro Tag.
In enger Zusammenarbeit mit dem Stern
Einer, der den Überblick über dieses logistische Puzzle hat, ist Geschäftsführer Frank Boblat: „Was wir hier machen, ist weit mehr als Lagerhaltung und Transport“, so der gelernte Maschinenbauer. Denn LOREL koordiniert im Plant Consolidation Center die Warenströme von Zulieferern auf dem Weg ins Mercedes-Benz Werk. Zwei Drittel der täglichen LKW-Fahrten werden vor Ort entladen, bei den übrigen Fahrten steuert LOREL die rechtzeitige und teilegenaue Anlieferung ans Werk durch andere Zulieferer. Darüber hinaus montieren die Angestellten in den Hallen Einzelteile zu Baugruppen, sodass die Mercedes-Bandarbeiterinnen und -arbeiter komplette Komponenten, wie zum Beispiel Mittelkonsolen, einbauen können. „Die Vormontage macht 30 Prozent unseres Gesamtgeschäfts aus und wächst stetig“, führt Boblat aus.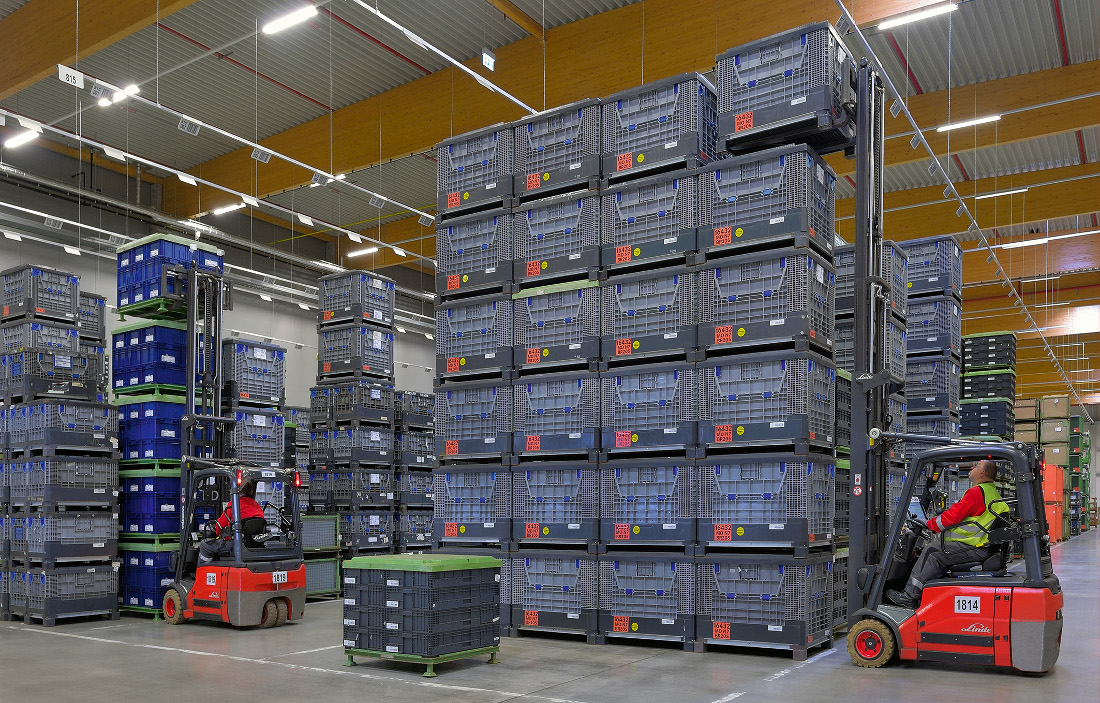
Die Gabelstapler stehen bei Lorel niemals still: Im 3-Schichtbetrieb sequenzieren Mitarbeiter Bauteile für das Band im Mercedes-Benz Werk © LOREL Logistik GmbH
Jedes Auto ist anders – und das macht Arbeit
Das Mercedes-Benz Werk arbeitet mit seiner Jahresproduktion von mehr als 400.000 Fahrzeugen an seiner Kapazitätsgrenze. Unternehmen wie LOREL übernehmen die Logistik und Vormontage, damit Mercedes-Benz die Produktion ausweiten kann. Grund dafür ist neben der gesteigerten Nachfrage auch die steigende Komplexität im Automobilbau. „Die Modellvielfalt wird größer, die Kunden haben immer individuellere Wünsche, die mehr Varianten, mehr Einzelteile und damit mehr Platzbedarf bedeuten“, so Boblat. Deshalb werden Teile der Mercedes-Produktion heute „just-in-sequence“ bedient – die Komponenten werden in der Reihenfolge auf die Ladungsträger sortiert, in der der Arbeiter sie am Band montieren muss. 2.500 verschiedene Ladungsträgertypen verwaltet LOREL – in einer eigenen Leerguthalle sortieren die Angestellten die aus dem Werk zurückkommenden Träger, um sie wieder auf den Weg zu den Zulieferern zu schicken. Sollte ein Träger kaputt gehen, wird er hier aussortiert und wieder instandgesetzt.Keine Zeit für Fehler
Die steigende Variantenvielfalt bedeutet für LOREL neben zusätzlicher Verantwortung vor allem höheren Logistikaufwand. Dazu kommt: Bevor ein Bauteil am Band eingebaut wird, erhält LOREL zeitnah die Teileanforderung aus dem Werk. Die Vorlaufzeit für den Versand in die Mercedes-Produktion beträgt lediglich eine Stunde. Ein extrem knapper Zeitraum. „Die Bestellung wird automatisch verarbeitet, sonst könnten wir das gar nicht schaffen. Wir dürfen uns keine Fehler leisten“, verdeutlicht Boblat. Aus diesem Grund sind etwa die Vormontage-Plätze genauso eingerichtet wie im Mercedes-Werk.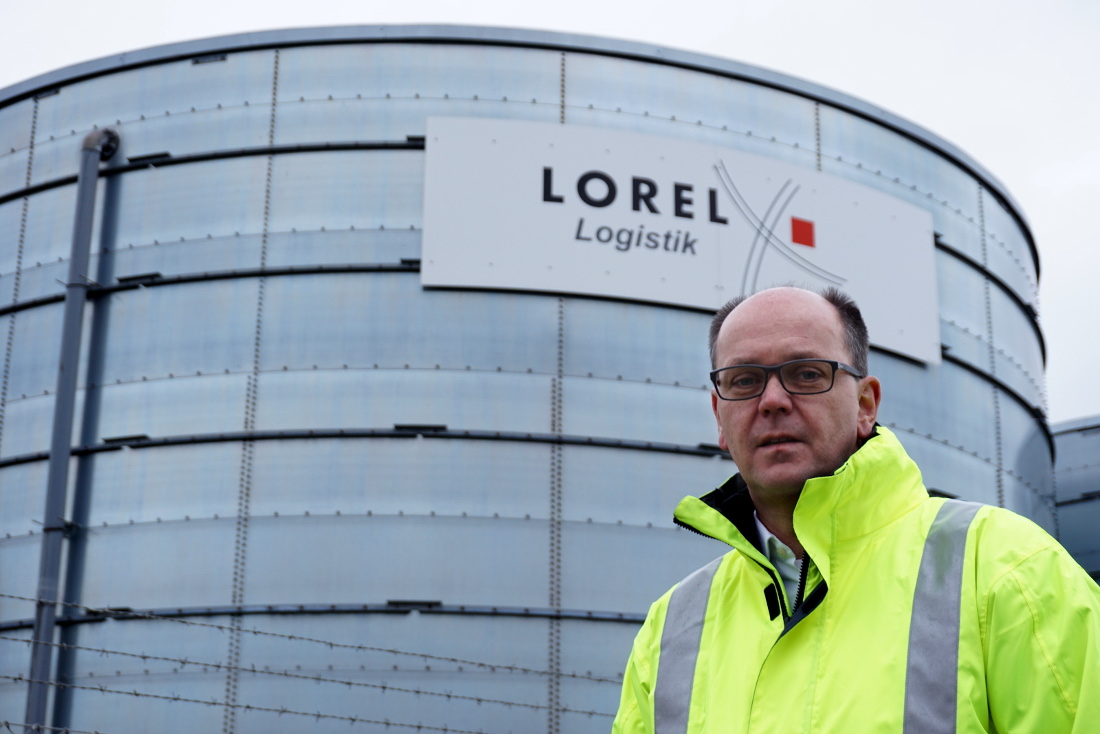
Geschäftsführer Frank Boblat © WFB/Raveling